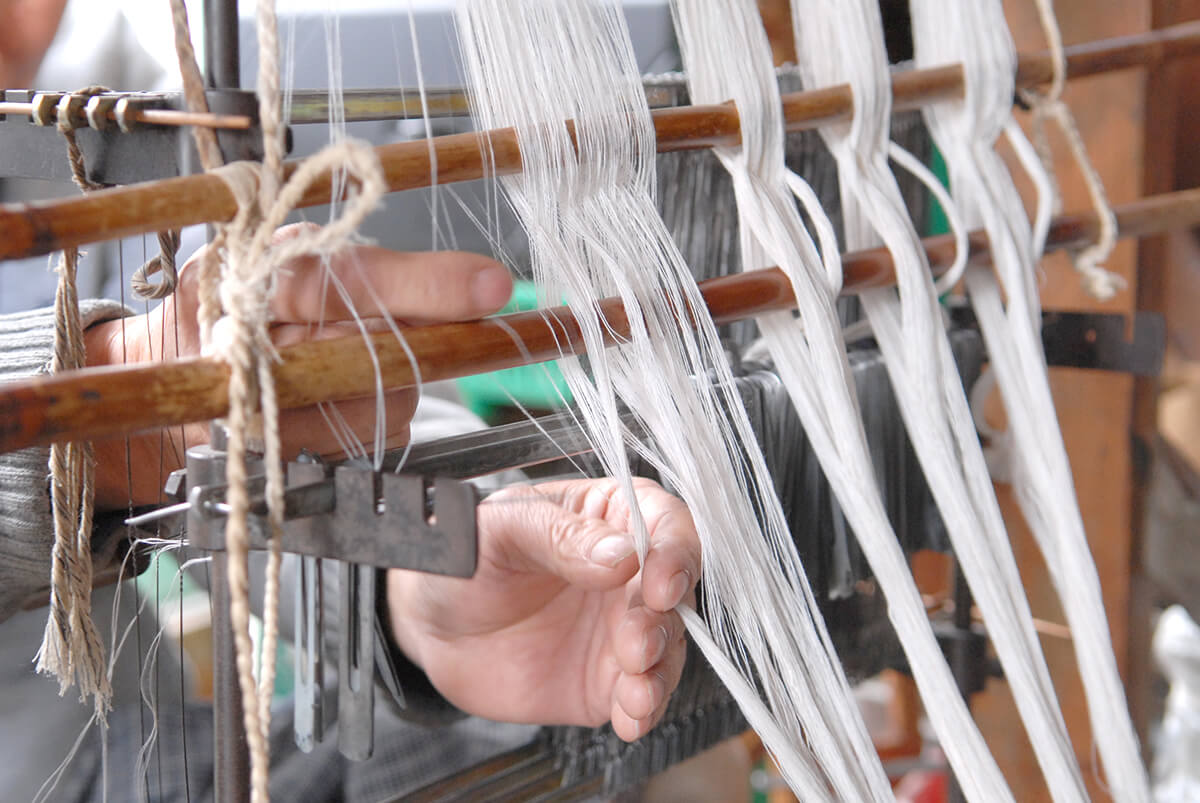
Transferred from people to people
“Loom weaving” in Hamamatsu City, Shizuoka Prefecture is said to have started in the Edo period as wintertime work for farmers. Weaving consists of various processes such as the spinning process to convert raw cotton into yarn and the dyeing process. It is said that each person involved in each step had his or her own specialty, and this developed into division of labor.
The Enshu Region, blessed with moderate climate and rich nature, is suitable for growing cotton and has flourished as one of Japan's three major cotton producing regions together with the Mikawa and Senshu Regions.
Power looms (weaving machine driven by motor) were introduced in the Meiji period by a loom manufacturer, known now as the Toyota Motor Corporation, and Suzuki Motor Corporation that is headquartered in Hamamatsu City. The golden age of the weaving industry was reached in the 1950’s (Showa 30’s). However, since 1989, production has continued to shrink and has been undermined by overseas products.
“Enshu Men Tsumugi,” hand-made by craftsmen, conveys our region’s heritage to the present and is now a rare and precious fabric. We cherish our tradition that has been passed down from generation to generation.
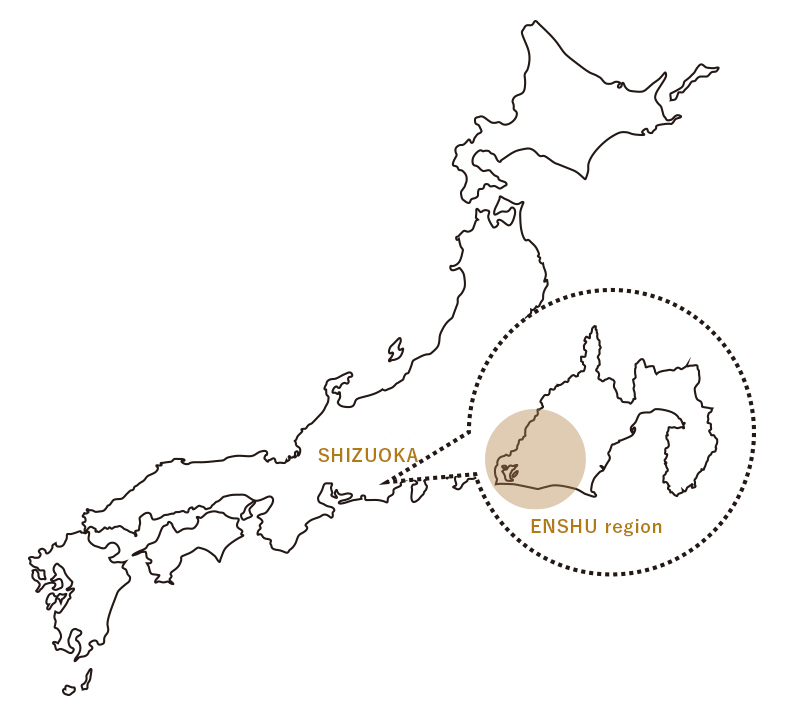
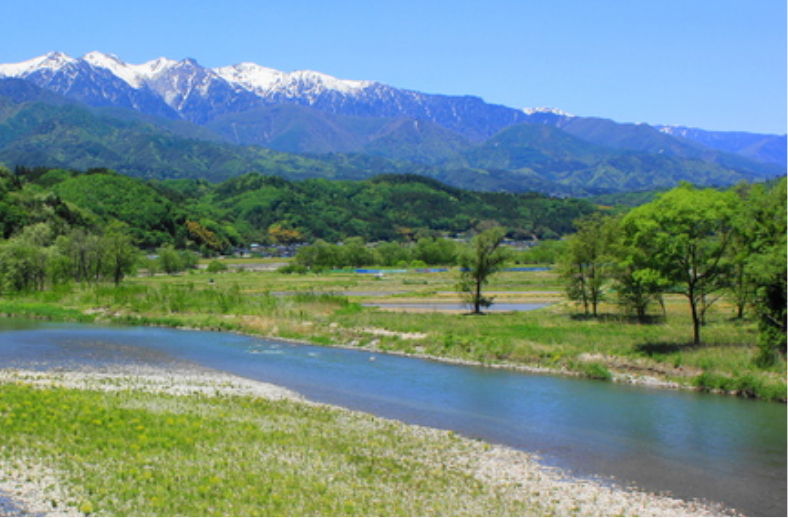
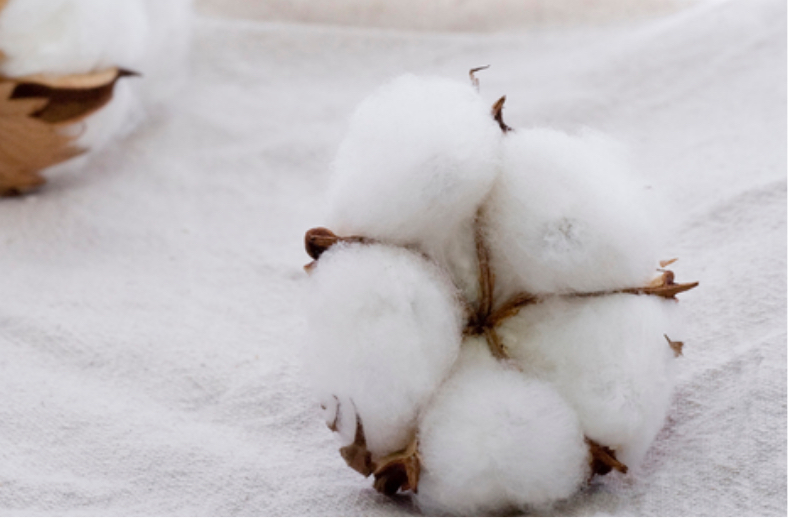
“You’ll be loved by a new family. You’ll be made into a beautiful cloth. As if I were marrying off my daughter. This is what I feel while weaving,” says a weaver. In each process until a fabric is finished, each craftsman preserves the tradition with pride by carefully and repeatedly performing their manual works by following the traditional methods. The feeling of warmth, nurtured by the craftsman’s hands, somehow seems nostalgic.
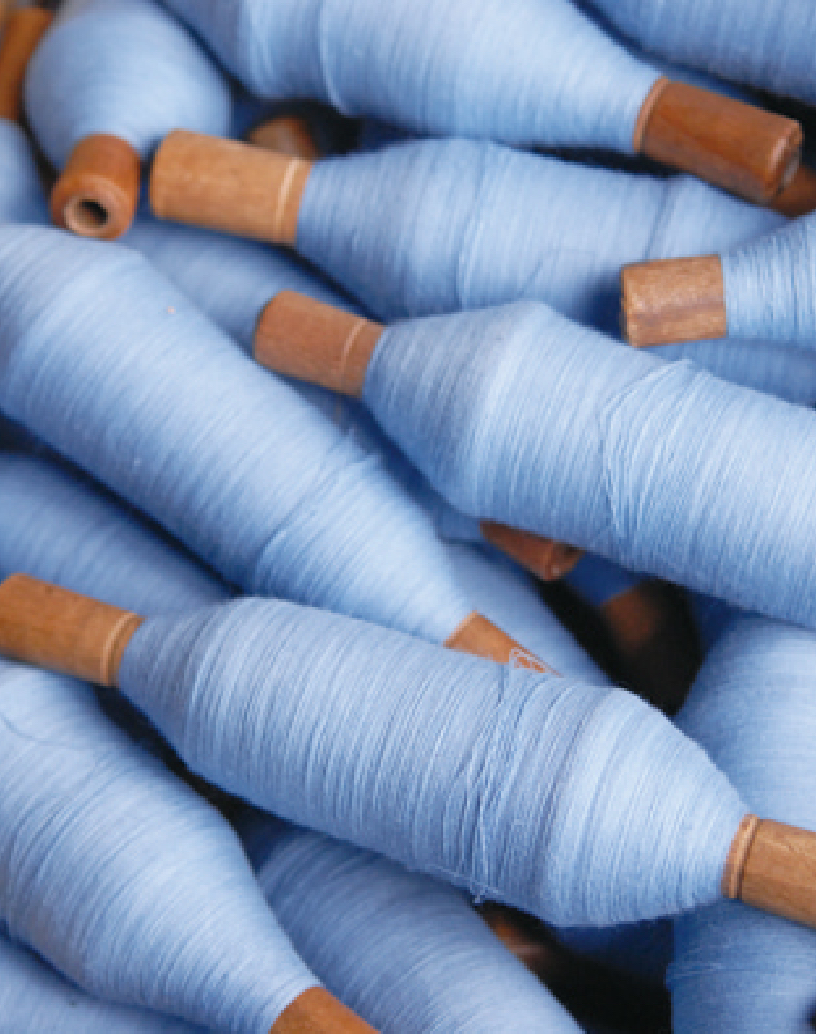
How Enshu Mentsumugi is created
Hank-winding
Cotton yarn to be the raw material for the cotton spindle is wound into a “kase (hank),” which is a bundle of a fixed length of yarn. While careful attention is paid so as to get a neat roll, a large volume of yarn is wound manually without stopping.
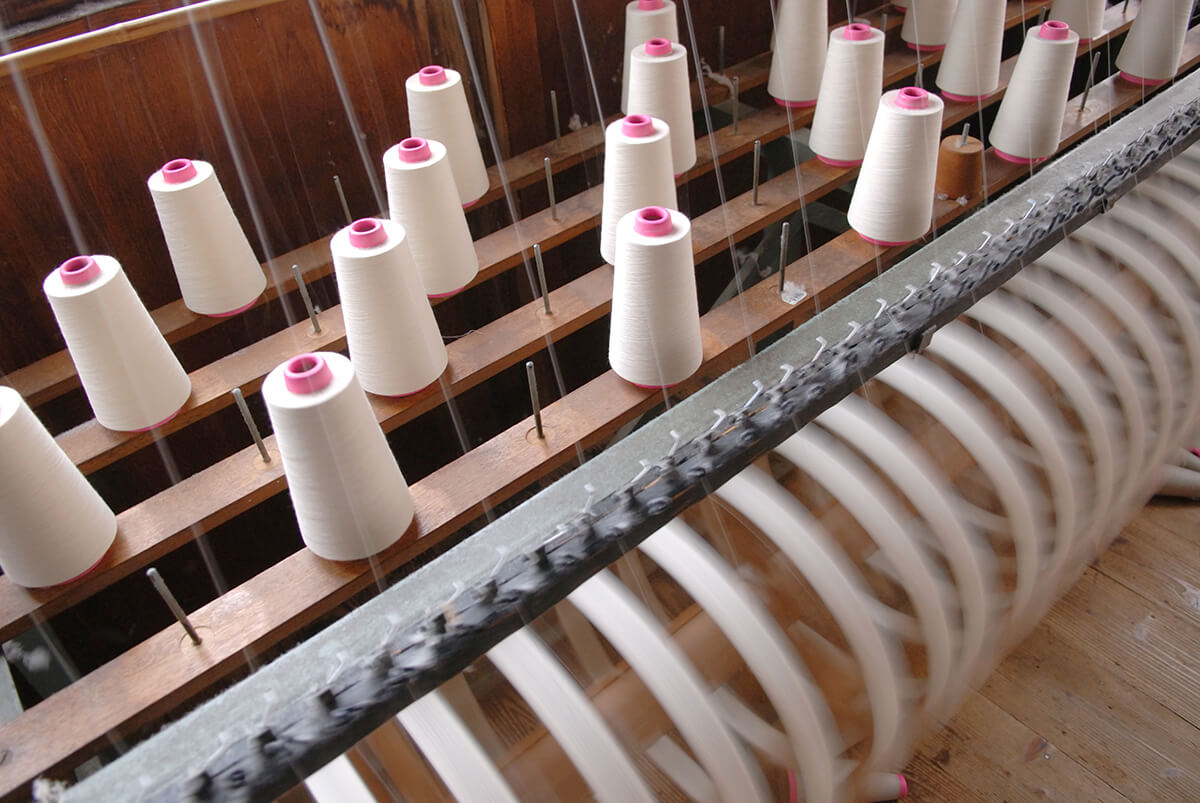
Dyeing
Yarn is bleached (refining) and then dyed a specified color. The yarn is first rinsed in hot water so that vegetable fat and lye are removed, making it easier for color to penetrate the yarn. The yarn is placed in a large pot, and hot water with the dye dissolved in it is poured over the yarn.
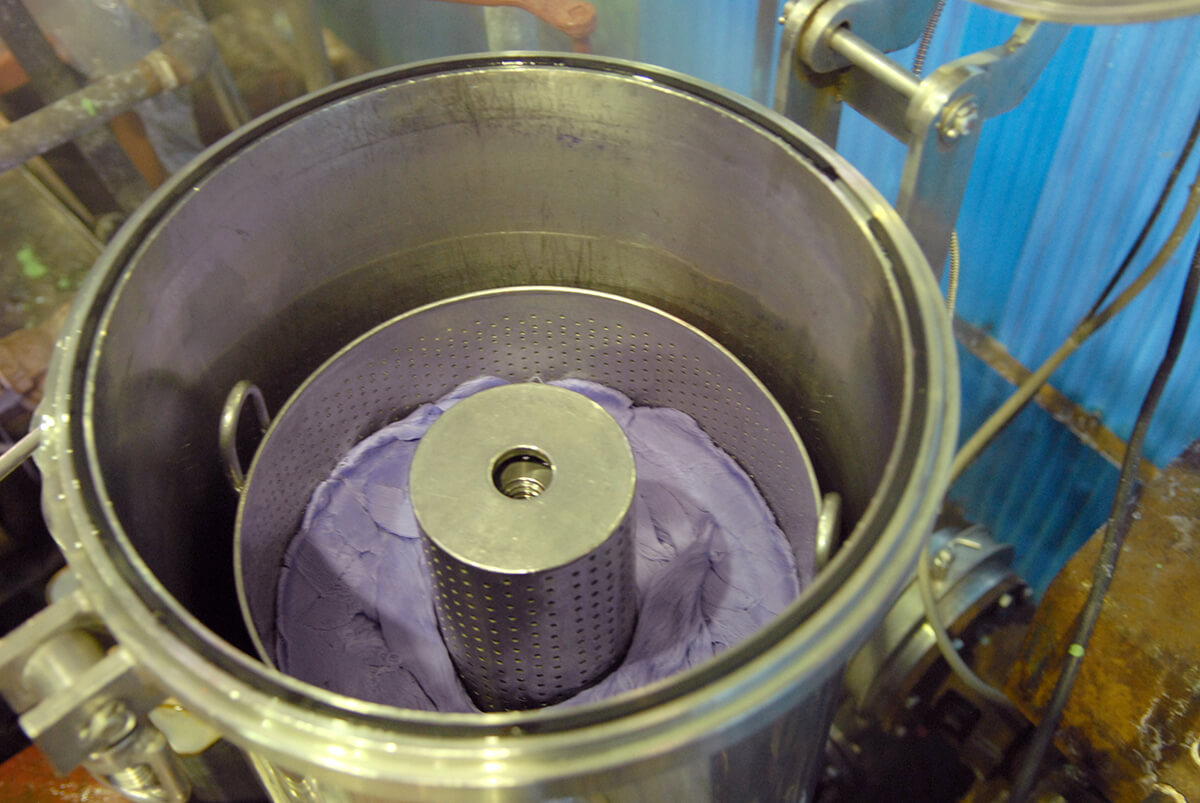
Starching
To prevent yarn from fluffing and to facilitate weaving, starch is impregnated into the yarn. This process serves to prevent yarn from being cut due to weaving friction. While the starch is kept warm, an adequate volume of yarn is immersed in it, mixed thoroughly and evenly and slightly fanned for settling.
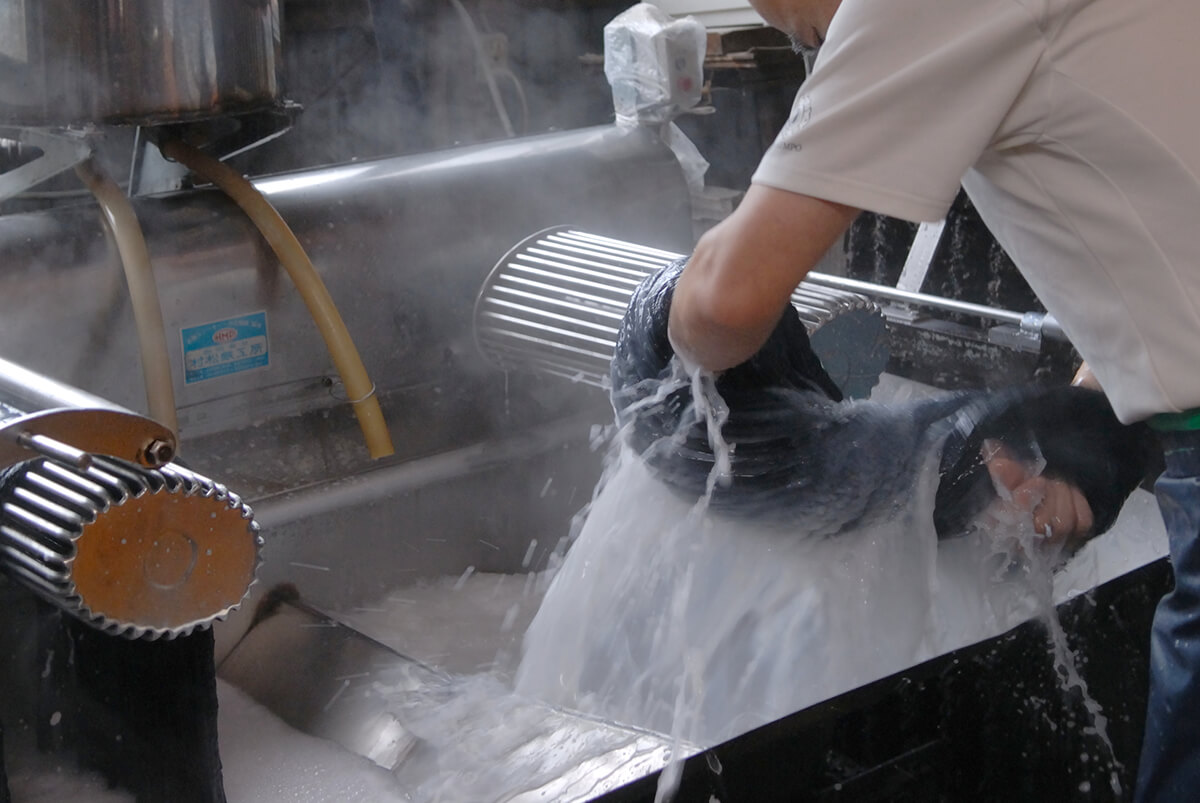
Pirn winding
The yarn bundle is then wound onto a pirn again. The hank of yarn, after being dyed and starched, is wound into a bundle called an “imokuda” (larger pirn state). The yarn is wound with great care to prevent the yarn from getting tangled or cut.
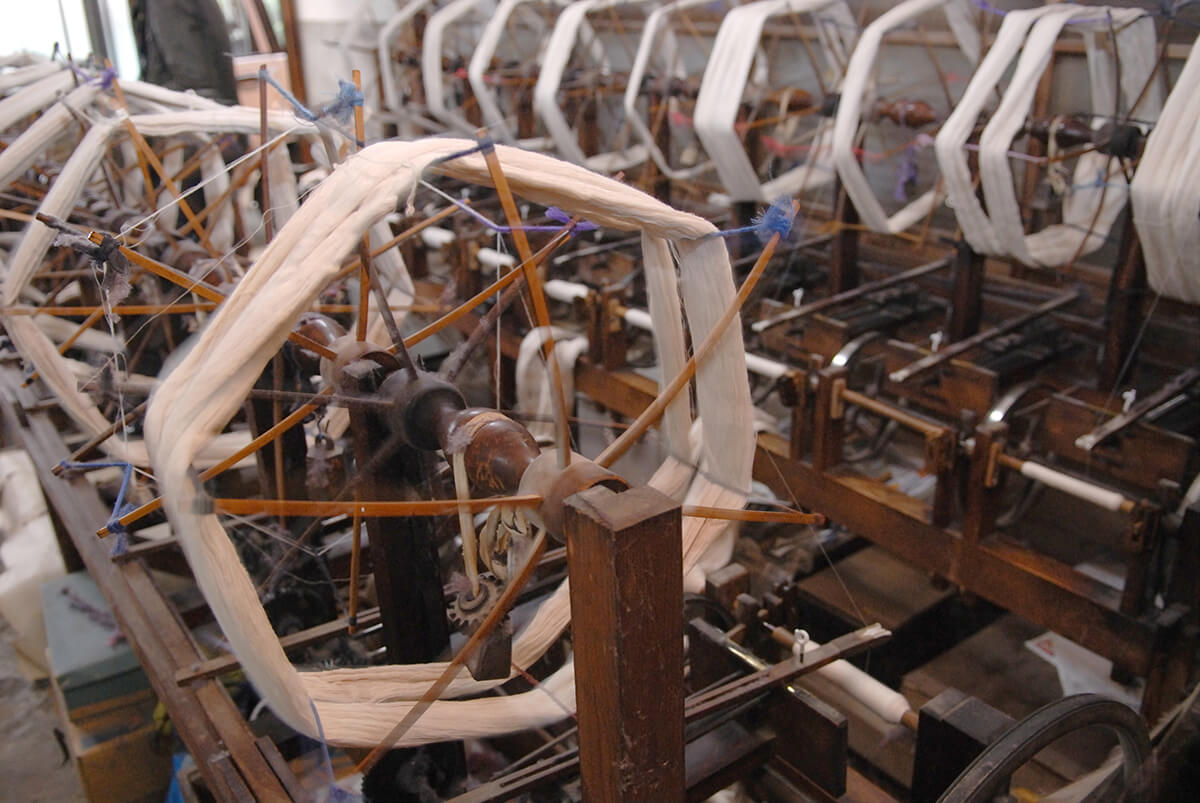
Warping
Warps are aligned according to the pattern. Each pattern has its own combination of the number of yarns and colors, which is fixed by the order of alignment.
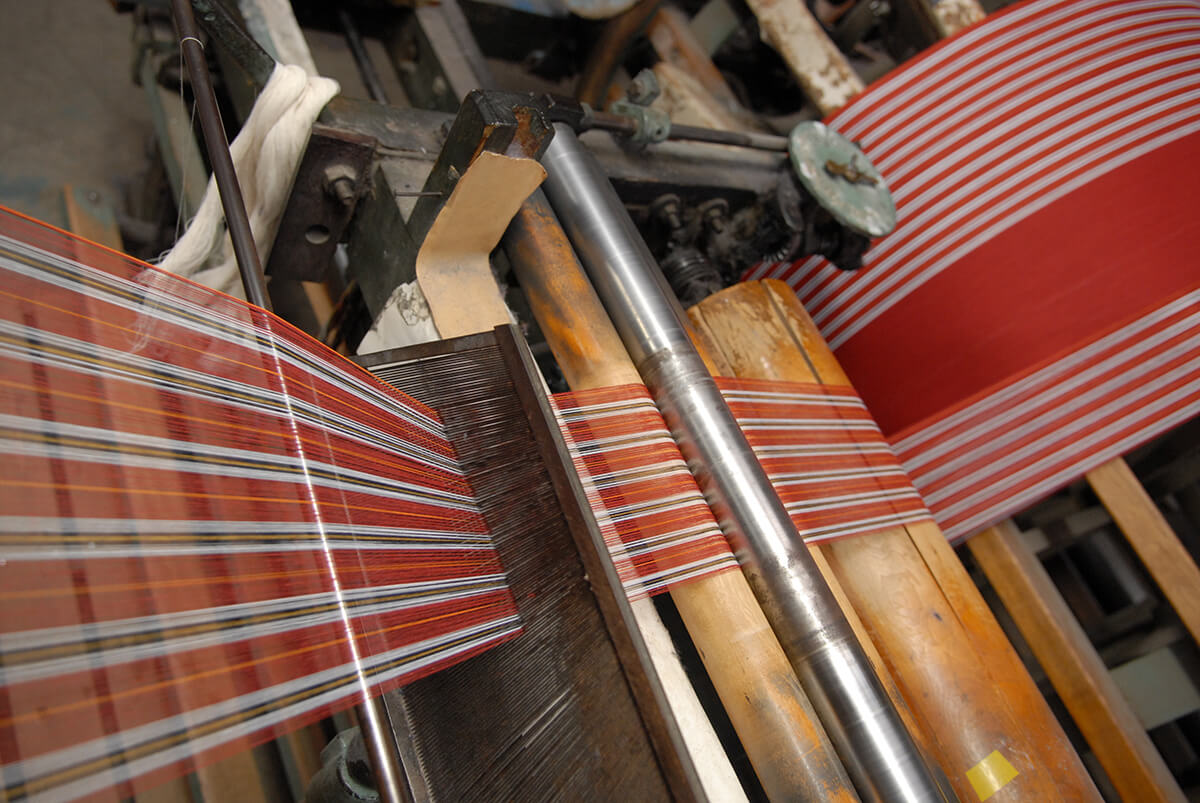
Reeding
The yarns aligned one by one in a pattern are passed through the comb-shaped holes called a “reed”. When Hetoshi is completed, yarns are wound all at once.
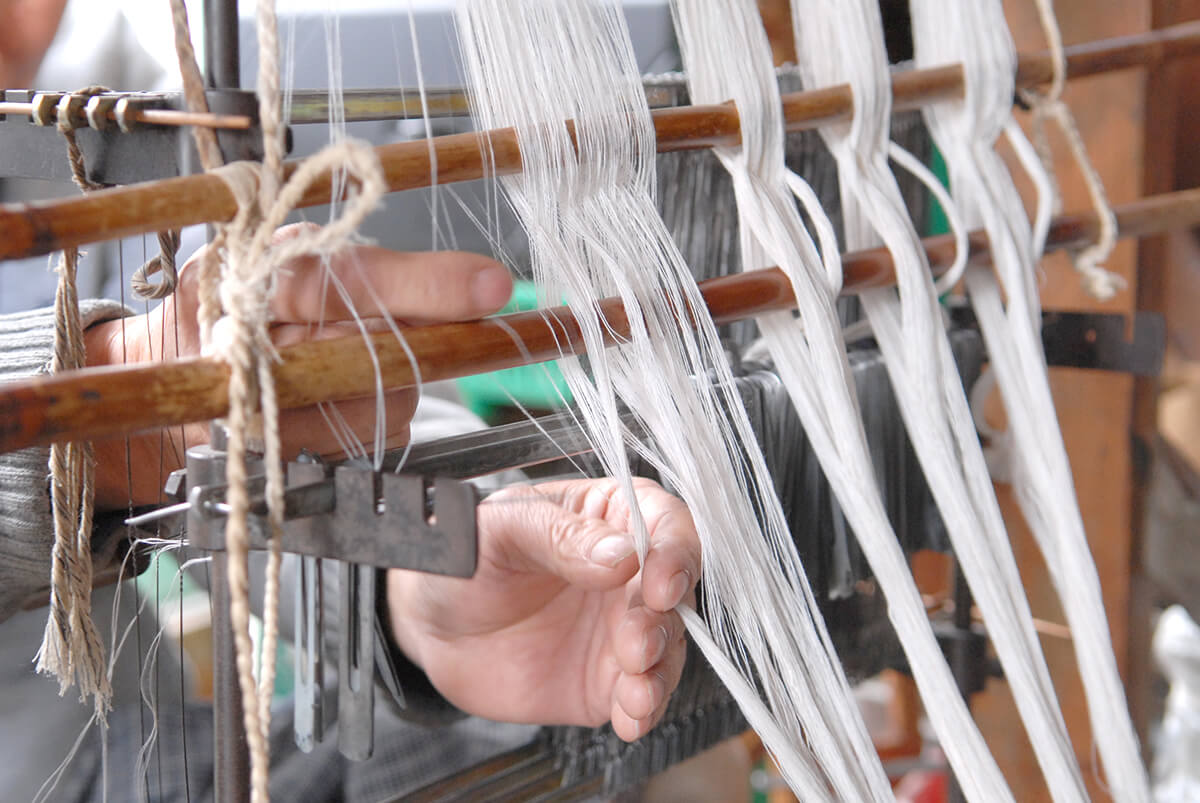
Weaving
The warps are fixed on the loom, and weaving operation starts.The final color shade depends on the colors used for the wefts. Approximately one to two tans of cloth per day (one tan is approximately 13m in length and 36cm in width) are carefully woven on the loom.
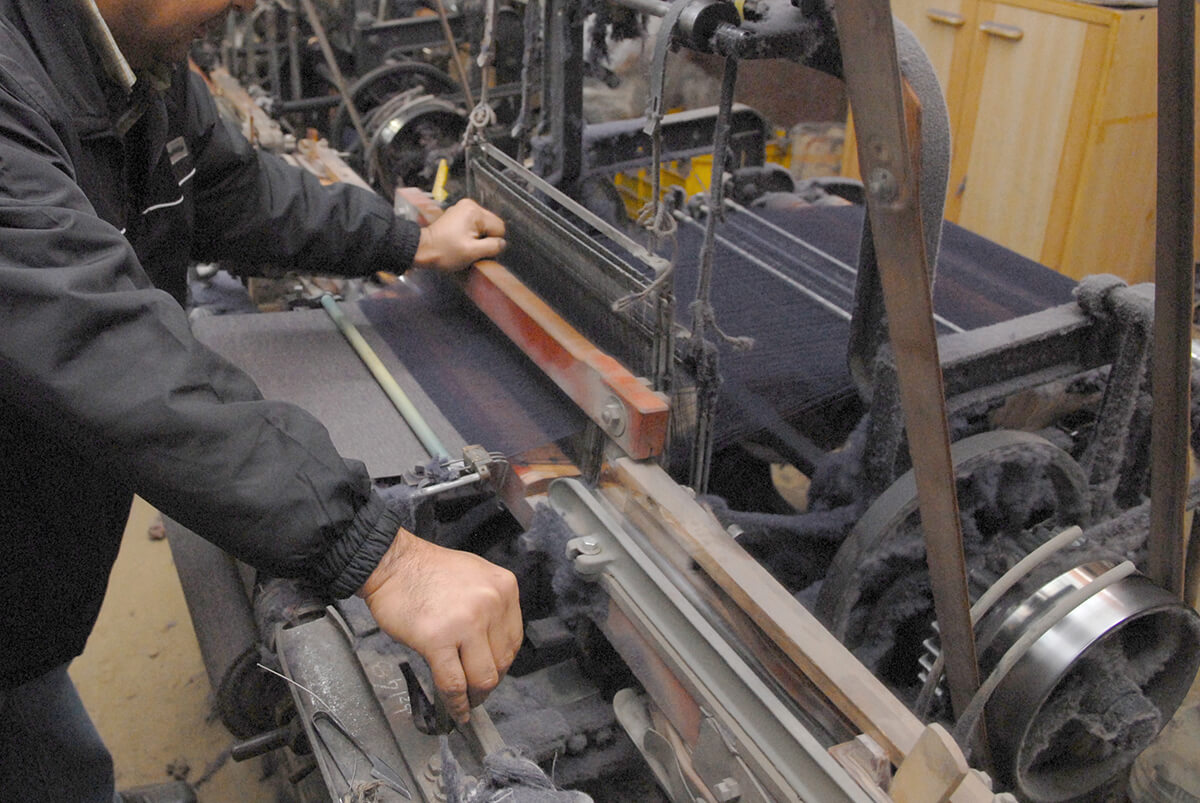
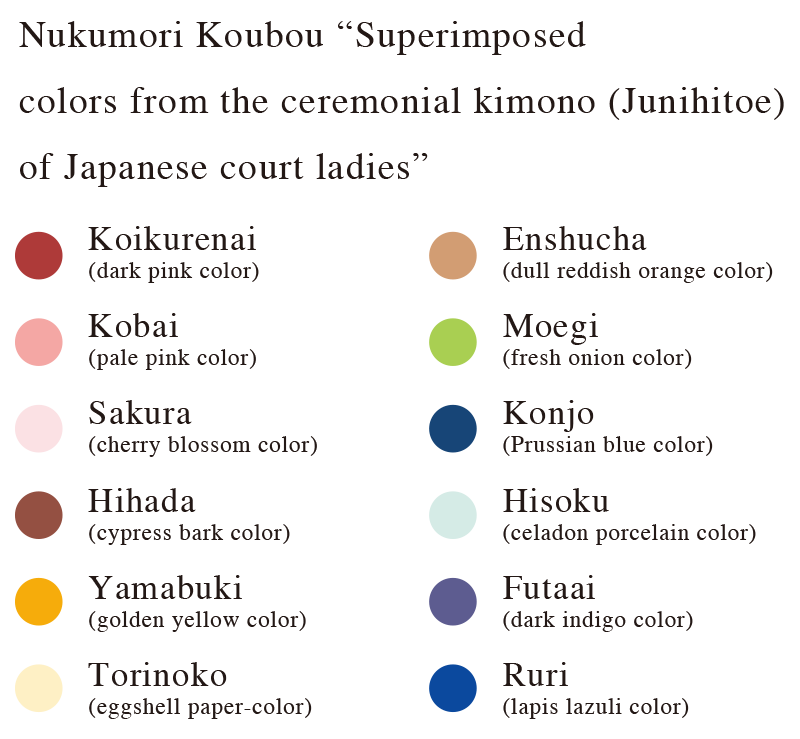
Ubuginu Shrine, located in Mikkabicho, Kita-ku, Hamamatsu, is dedicated to Orihime (goddess of weaving), known to all Japanese people from the legend of Tanabata or the Star Festival. From the end of the Heian period more than 850 years ago, silk garments have been woven for offering to the gods at the Kotai Jingu (the Inner Shrine) in Ise Shrine every year.
The legend says that Orihime wove the silk Tsumugi fabric used in these garments (called Onzo). The material was later changed from silk to cotton, and the Enshu Region developed into a major cotton textile-producing area. Nukumori Koubou Craft Center is located in an area associated with Orihime, and where “Enshu Men Tsumugi”, the traditional fabric of Hamamatsu, has been inherited.
The logo is designed in the motif of Ubuginu Shrine's Torii gate, using the 12 traditional Japanese colors used for the “layered colors of Junihitoe (twelve-layered ceremonial kimono)”. These colors create the “striped pattern” characteristic of Enshu Men Tsumugi.